“Understanding SPC: What You Need to Know About SPC and Its Applications”
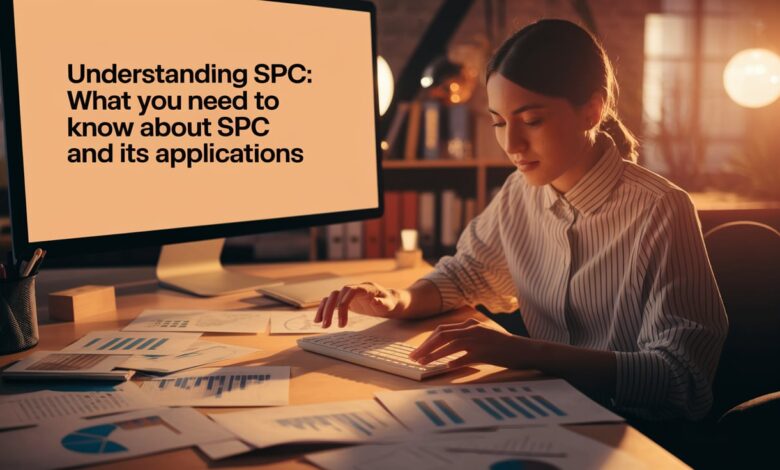
SPC stands for Statistical Process Control, a method used in quality management to monitor and control processes. The goal of SPC is to ensure that a process is operating efficiently and producing products that meet quality standards. This technique is widely used in manufacturing industries to maintain product consistency and improve production efficiency. By tracking data from a production line or system, businesses can identify variations in the process and take corrective actions before defects occur. SPC helps companies maintain high standards, reduce waste, and improve customer satisfaction. It’s an essential tool for businesses that want to stay competitive in today’s fast-paced market.
SPC involves collecting data from various points in the production process and analyzing it using statistical methods. By doing so, manufacturers can identify patterns and trends that might indicate problems or inefficiencies in the process. This allows businesses to make informed decisions based on real data rather than assumptions. For example, if a machine is producing parts that are out of specification, SPC data will help identify the issue early, reducing the likelihood of producing defective products. In this blog post, we’ll explore how SPC works, why it’s so important, and how you can implement it in your business to boost performance and quality.
What is SPC: A Simple Guide to Statistical Process Control
Statistical Process Control (SPC) is a method used to monitor and control a process through data collection and analysis. This system helps businesses maintain consistent product quality by tracking variations in the manufacturing process. It uses statistical tools like control charts to determine whether a process is stable or needs adjustment. SPC aims to detect problems early, which prevents defects before they affect the end product. By analyzing patterns and trends in production data, businesses can take timely corrective actions to keep the process running smoothly. With SPC, companies improve efficiency, reduce waste, and enhance overall quality, making it an essential tool in today’s competitive manufacturing world.
The Role of SPC in Improving Product Quality and Efficiency
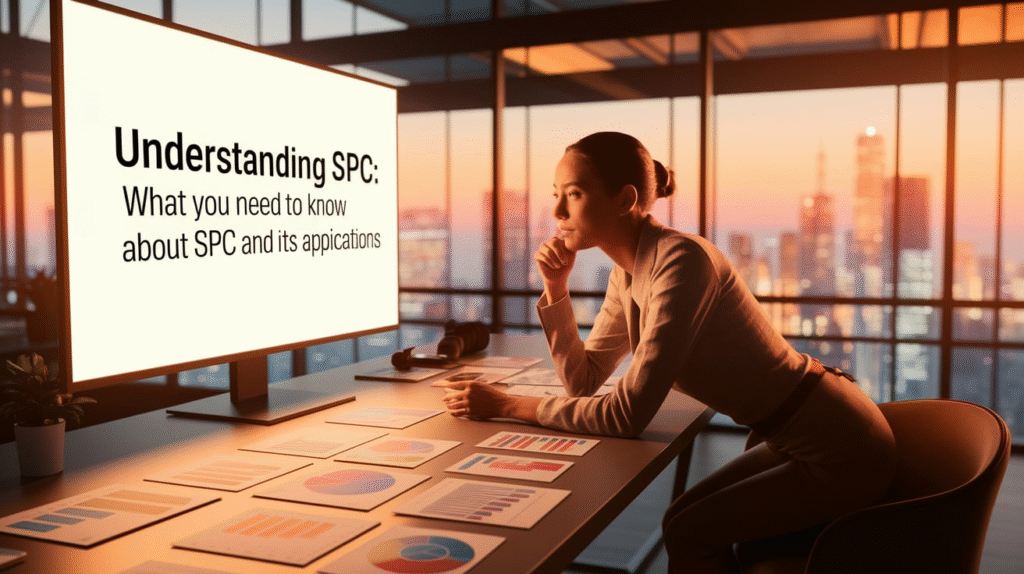
SPC plays a crucial role in improving product quality by identifying any variations in the production process. By consistently monitoring the process, SPC helps businesses spot issues before they become serious problems. This early detection allows for quick interventions, ensuring that the final product meets the desired quality standards. With SPC, manufacturers can eliminate unnecessary waste, reduce the risk of defects, and keep production running efficiently. Additionally, SPC helps in optimizing workflows, which improves overall efficiency. When employees understand the process and the metrics that measure it, they can contribute to a more reliable production environment. As a result, SPC not only ensures top-notch product quality but also supports long-term business growth.
How SPC Can Help Your Business Reduce Waste and Improve Profits
SPC helps businesses reduce waste by identifying inefficiencies in their processes before they lead to defects. By analyzing data and monitoring key performance indicators, companies can spot variations that could result in product rejections, overproduction, or other types of waste. Early identification of these issues allows businesses to take corrective actions that improve the efficiency of their operations. Reduced waste means lower costs and higher profit margins, as businesses can produce more with less. SPC also helps streamline production processes, which results in faster turnaround times and fewer bottlenecks. Ultimately, using SPC for waste reduction not only boosts profitability but also contributes to environmental sustainability, making it an excellent choice for businesses focused on continuous improvement.
Top Benefits of SPC for Small and Medium Enterprises
Small and medium enterprises (SMEs) can greatly benefit from implementing SPC in their operations. One of the main advantages is the ability to enhance product quality without the need for costly overhauls. SPC helps SMEs catch problems early, saving time and money in the long run by preventing defects that could harm the business. Additionally, SPC allows SMEs to reduce waste, optimize processes, and increase production efficiency, which are crucial for staying competitive in a fast-paced market. By providing data-driven insights, SPC empowers businesses to make informed decisions that lead to better resource management and cost control. For SMEs looking to scale their operations, SPC is an effective tool for achieving consistent growth and maintaining high standards.
Step-by-Step Guide to Implementing SPC in Your Manufacturing Process
Implementing SPC in your manufacturing process starts with defining key quality metrics and collecting data on your current processes. Begin by selecting the critical points in the production line where variations are most likely to occur. Next, use control charts and other statistical tools to analyze the data and establish control limits. Once you’ve set benchmarks, regularly monitor the process and look for any signs of instability or deviations from the norm. If issues arise, take immediate corrective actions to bring the process back within control. It’s also important to train staff on SPC principles so they can actively participate in maintaining quality standards. By following these steps, you’ll create a more efficient and consistent production environment.
SPC vs. Traditional Quality Control: What’s the Difference
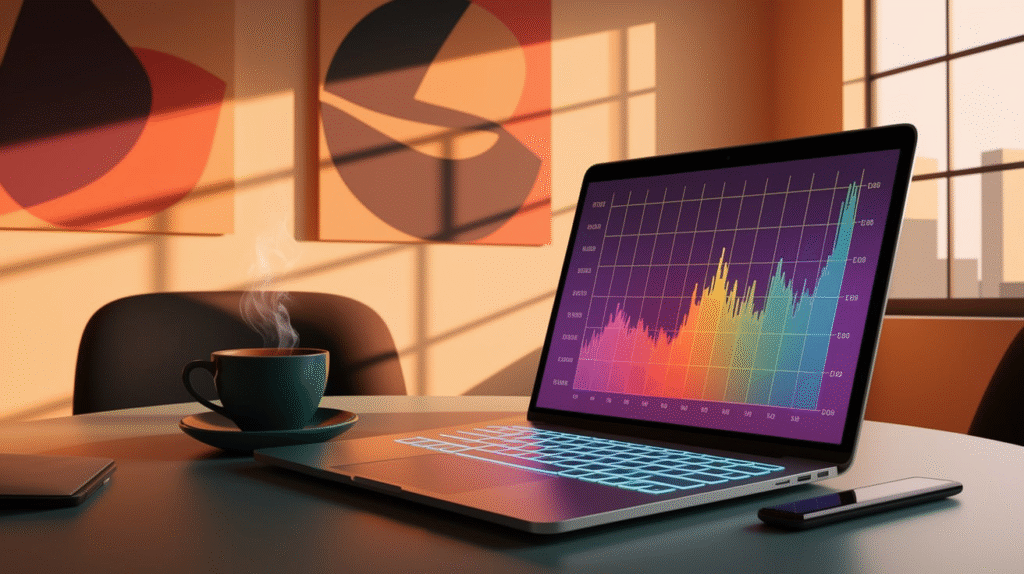
SPC and traditional quality control (QC) both aim to maintain high-quality standards, but they differ in their approaches. Traditional QC typically involves inspecting finished products for defects, which may not catch problems that occur during the production process. SPC, on the other hand, continuously monitors the production process in real-time, using data analysis to detect variations and prevent defects before they occur. While QC is reactive, SPC is proactive, allowing companies to address issues before they lead to defective products. SPC provides a more comprehensive approach by focusing on improving the process itself, rather than just inspecting the end result. As a result, SPC is considered a more efficient and long-term solution for quality control.
The Key Tools Used in SPC: From Control Charts to Process Monitoring
SPC uses several key tools to monitor and control production processes. The most common tool is the control chart, which displays data over time and helps identify trends and variations in the process. Another essential tool is the process capability index, which measures how well a process can produce products within specifications. Other tools used in SPC include histograms, Pareto charts, and scatter diagrams, which provide different ways to analyze and interpret data. Process monitoring techniques, such as real-time data tracking and feedback loops, help ensure that the process stays on track. By using these tools, businesses can gain a deeper understanding of their processes and make data-driven decisions to improve quality and efficiency.
How SPC Helps Prevent Defects Before They Happen
One of the biggest advantages of SPC is its ability to prevent defects before they happen. By continuously monitoring production processes and analyzing data, SPC identifies small variations that may lead to defects if left unchecked. These early warnings allow manufacturers to make adjustments quickly, ensuring that the process remains within control. Whether it’s adjusting machine settings, altering production speeds, or changing materials, SPC helps manufacturers take proactive steps to correct issues before they result in defective products. This not only reduces scrap and rework costs but also enhances customer satisfaction by ensuring that products meet quality standards. In the long run, SPC helps create a culture of continuous improvement that reduces the likelihood of defects over time.
Understanding the Core Principles of SPC and How They Apply to Your Business
The core principles of SPC revolve around the idea of continuous process improvement through data analysis and control. The main goal is to detect and reduce variation in the production process, ensuring that products meet quality standards consistently. SPC emphasizes using statistical tools to analyze data collected during production and taking corrective actions when necessary. By focusing on process stability, SPC helps businesses achieve predictable outcomes, making it easier to maintain product quality. Applying SPC to your business involves understanding where variation occurs, measuring it, and taking action to reduce it. This approach not only improves quality but also leads to cost savings and higher customer satisfaction by ensuring consistent product outcomes.
How to Use SPC Data to Drive Continuous Improvement in Your Business
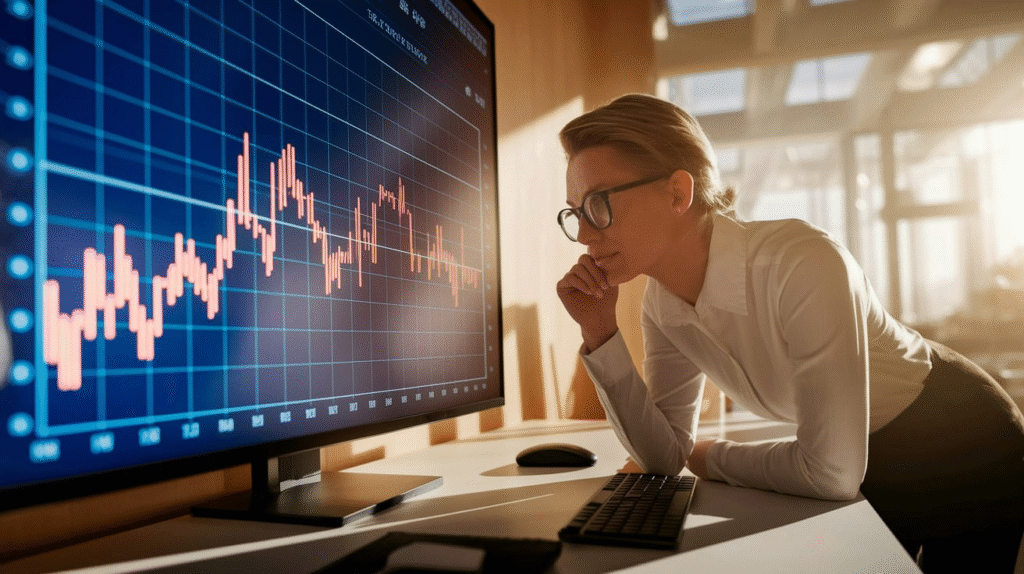
SPC data is a powerful tool for driving continuous improvement in your business. By regularly analyzing production data, you can identify areas where processes can be optimized for better quality, efficiency, and cost control. SPC data helps pinpoint specific issues, such as equipment malfunctions or inconsistent raw materials, that may impact production. With this information, you can implement corrective measures to fix the problem before it escalates. Over time, SPC data allows you to track the impact of improvements and refine processes further. Using this data-driven approach, businesses can foster a culture of continuous improvement, ensuring long-term success and a steady path toward enhanced product quality and operational excellence.
Conclusion
SPC (Statistical Process Control) is a powerful tool that helps businesses improve product quality, reduce waste, and increase efficiency. By monitoring processes and using data to detect problems early, SPC allows companies to fix issues before they lead to defects. This makes it a crucial method for businesses that want to stay competitive and produce high-quality products consistently. It’s not just for big companies – even small businesses can benefit from using SPC to improve their operations.
By implementing SPC in your business, you can create a smoother, more efficient production process. It will help you save time, money, and resources while ensuring that your products meet high-quality standards. As you keep track of your production and continuously improve, you’ll see better results over time. SPC helps businesses grow, improve, and succeed by making informed decisions based on data.
FAQs
Q: What is SPC?
A: SPC stands for Statistical Process Control, a method used to monitor and improve the quality of products during production using data analysis.
Q: How does SPC help businesses?
A: SPC helps businesses identify problems early, reduce waste, improve efficiency, and maintain high-quality standards in their products.
Q: Do I need special tools for SPC?
A: Yes, tools like control charts and data tracking software are commonly used to analyze and monitor processes in SPC.
Q: Can SPC be used in small businesses?
A: Absolutely! SPC is helpful for businesses of all sizes and can help small businesses improve their processes and reduce costs.
Q: How often should SPC be used?
A: SPC should be used regularly, as it monitors data continuously and helps spot variations in real-time, allowing for quick adjustments when needed.